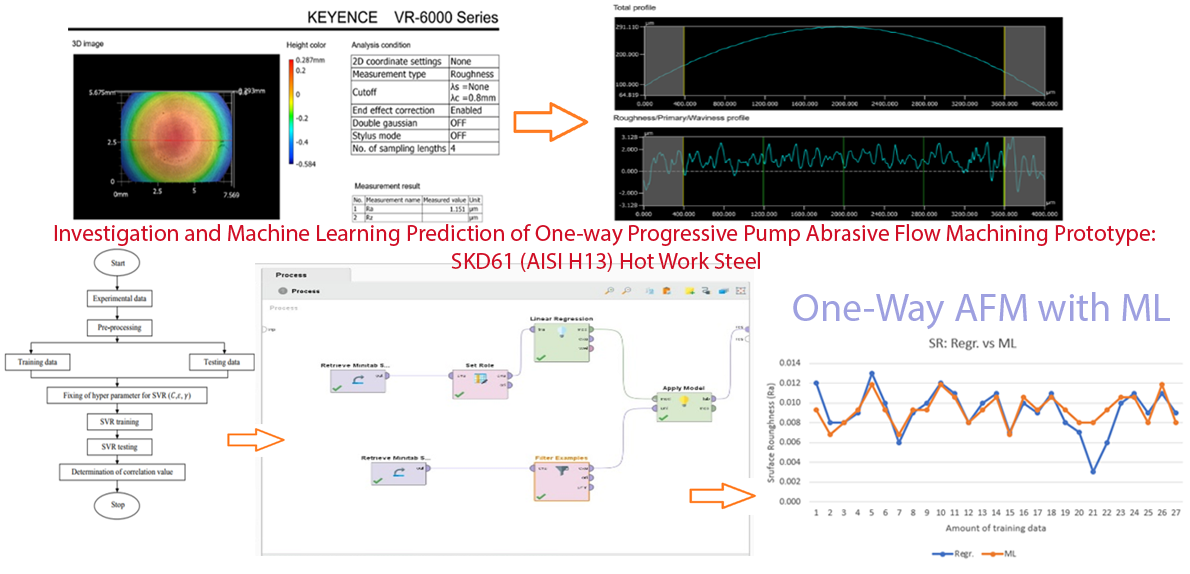
Theerapong Maneepen
Program in Engineering and Technology Management, Faculty of Engineering, Rajamangala University of Technology Krungthep, 10120 Thailand
https://orcid.org/0000-0003-3991-9850
Parinya Srisattayakul
Department of Industrial Engineering, Faculty of Engineering, Rajamangala University of Technology Krungthep, 10120 Thailand
DOI: https://doi.org/10.14456/apst.2025.52
Keywords: Abrasive Flow Machining Surface Roughness Design of Experiment Machine Learning
Abstract
The objectives are to study the effects of tooling pressure and machining time on surface roughness regulatory affairs (Ra) of hot work steel SKD 61 involving an abrasive flow machining (AFM) polishing prototype and to compare the design of experiments (DOE), factorial regression, and predictive machine learning (ML). The research steps include defining the objectives, identifying the important factors and their levels, designing the experiments, conducting experiments and collecting data, and analyzing the results statistically. The ML process was performed with a program, the experimental results were compared and concluded. A progressive pump (NETZSCH) was used to conduct the experiments on the AFM curved samples. Experiments were conducted to investigate machined, hardened, polished samples with abrasive papers from #180 to #1200 and were measured with the initial Ra values against the final value. The process parameters were pressure 1, 2, and 3 bar; sample hardness SKD61; 45±2 HRC; abrasive particle size (Al2O3) 5.0 microns (μm) (concentration 50% by weight, silicone oil). The results showed that 3 bar and 20 min, pressure, and cycle time consequently gave the best results. The average Ra of the workpieces was 0.057 to 0.042 microns, and the delta between surface roughness (SR) was 0.006 to 0.012 μm. The comparison of experimental and prediction results using RapidMiner ML showed only minor differences, indicating better precision control for industrial applications.
How to Cite
Maneepen, T., & Srisattayakul, P. (2025). Investigation and machine learning prediction of one-way progressive pump abrasive flow machining prototype: SKD61 (AISI H13) hot work steel. Asia-Pacific Journal of Science and Technology, 30(04), APST–30. https://doi.org/10.14456/apst.2025.52
References
Nitin Dixit, Varun Sharma, Pradeep Kumar. Research trends in abrasive flow machining: A systematic review. J Manuf Process. 2021;64: 1434-1461.
J.J. Hann, P.S. Steif. Abrasive wear due to the slow flow of a concentrated suspension, Wear.1998; 219:177-183.
Rajendra K. Jain, Vijay K. Jain, P.M. Dixit. Modeling of material removal and surface roughness in the abrasive flow machining process. Int J Mach Tools Manuf.1999; 39: 1903-1923.
V.K. Jain, and S.G. Adsul. Experimental investigations into abrasive flow machining (AFM). Int J Mach Tools Manuf. 2000; 49: 1003-1021.
Jun Wang, William Scott, Liangchi Zhang. Abrasive technology: current development and applications I, World Scientific. Singapore. 1999;2: 269-317.
Sehijpal Singh, H.S. Shan, P. Kumar. Wear behavior of materials in magnetically assisted abrasive flow machining. J Materials Process Technol. 2002;128(1–3):155–161.
P.D. Kamble, et al. Use of magneto abrasive flow machining to increase material removal rate and surface finish, Mechanical. Automobile Product Eng. 2012; 2: 249-262.
Kim JD, Kim KD. Deburring of burrs in spring collects by abrasive flow machining. Int J Adva Manuf Technol. 2004;24: 469-473.
Sankar MR, et. al. Experimental investigations into rotating workpiece abrasive flow machining. Wear. 2009:267: 43-51.
Jain R.K, Jain V.K, Kalra P.K. Modeling of abrasive flow machining process: a neural network approach. Wear. 1999; 231:242-248.
WANG AC, et al. Uniform surface polished method of complex holes in abrasive flow machining. Trans Nonferrous Met Soc China. 2009;19: 250-257.
Uhlmann E, et al. CFD simulation of the abrasive flow machining process. Procedia CIRP. 2015;31: 209-214.
Kumar S, et al. Nanofinishing of freeform surfaces (knee joint implant) by rotational-magnetorheological abrasive flow finishing (R-MRAFF) process. Precis Eng. .2015;42: 165-178.
Sharma VK, Modeling and analysis of a novel rotational magnetorheological abrasive flow finishing process. Int J Lightweight Mater Manuf. 2021;4: 290-301.
Kenda J, et al. Surface integrity in abrasive flow machining of hardened tool ateel AISI D2. Procedia Eng. 2011;9: 172-177.
Bahre D, et al. Investigation of one-way abrasive flow machining and in-process measurement of axial forces. Procedia CIRP. 2012; 1:419-424.
Swat M, et al. Improved process control and model of axial forces of one-way abrasive flow machining. Procedia CIRP. 2014; 14:19-24.
Bremerstein T, et al. Wear of abrasive media and its effect on abrasive flow machining results. Wear 2015;1: 44-51.
Wang AC, et al. A study on the abrasive gels and the application of abrasive flow machining in complex-hole polishing. Procedia CIRP. 2018; 68: 523-528.
Venkatesh G, et al. Finishing of bevel gears using abrasive flow machining, Procedia Eng. 2014; 97: 320-328.
Venkatesh G, et al. On ultrasonic assisted abrasive flow finishing of bevel gears. J Mach Tools Manuf. 2015; 89: 29-38.
Uhlmann E, et al. A pragmatic modeling approach in abrasive flow machining for complex-shaped automotive components. Procedia CIRP. 2016; 64: 51-54.
Chaneac MSD, et al. Characterization of maraging steel 300 internal surface created by selective laser melting (SLM) after abrasive flow machining (AFM). Procedia CIRP. 2018; 77: 359-362.
Han S, et al. Surface integrity in abrasive flow machining (AFM) of internal channels created by selective laser melting (SLM) in different building directions. Procedia CIRP. 2020;87: 315-320.
Dixit N, Sharma V, Kumar P, Experimental investigations into abrasive flow machining (AFM) of 3D printed ABS and PLA parts. Rapid Prototyp J. 2022;28(1):161-174.
Baraiya R, et al. In-situ simultaneous surface finishing using abrasive flow machining via novel fixture. J Manuf Process. 2020; 50: 266-278.
Han S, et al. Surface integrity in abrasive flow machining (AFM) of internal channels created by selective laser melting (SLM) in different building directions. Procedia CIRP. 2020; 87: 315-320.
Basha SM, et al. Development and performance evaluation of galactomannan polymer-based abrasive medium to finish atomic diffusion additively manufactured pure copper using abrasive flow finishing. Additive Manuf. 2023; 61: 103-290.
Ansari IA, et al. Effect of ground tire rubber media’s viscoelasticity and flow passage geometry on the abrasive flow finishing of helical gear. J Manuf Process. 2023;101: 219-233.
Dong X, et al. Fine finishing of internal surfaces using cassava starch medium. J Mater Process Technol. 2023; 315: 117918.
Lomozik L, et al. Optimization of WEDM parameters using machine learning: a comparative analysis of selected regression models. Int J Modern Manufa Technol. 2023; 15(2): 2067–3604.
Wasif M, et al. Prediction of spring back using the machine learning technique in high-tensile strength sheet metal during the V-bending process, Jordan J Mech Ind Eng. 2023; 17: 481-488.
Ismail FB, et al. A machine learning approach for fire-fighting detection in the power industry. Jordan J Mech Ind Eng.2021; 15(5): 475-482.
Rodjanaburanon N. Data analysis manual: Rapid Miner Studio.2022; 1: 9-45.
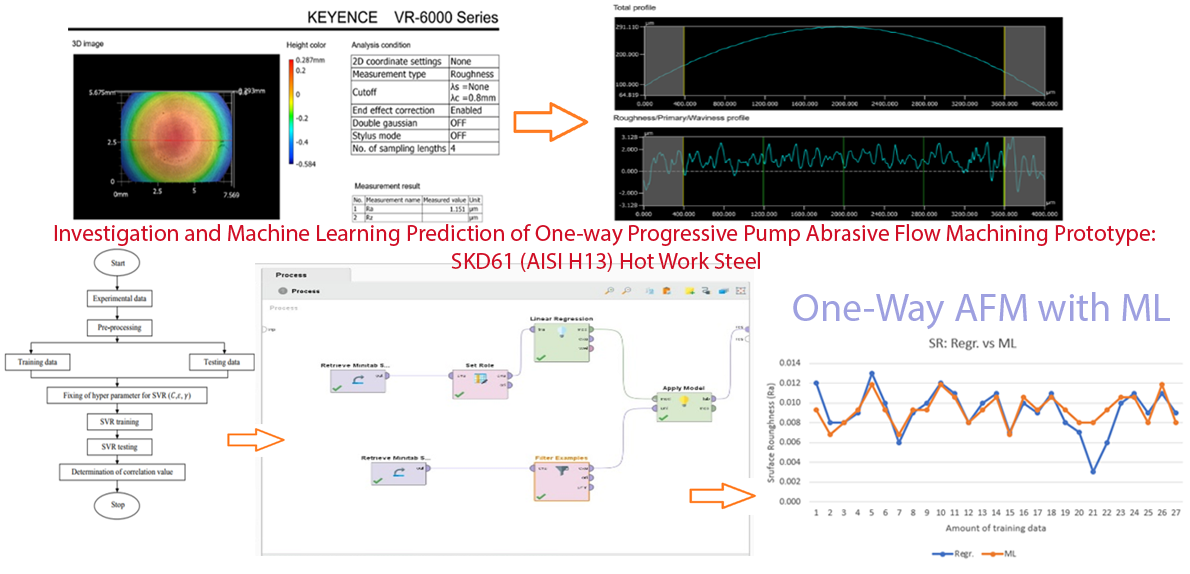
Published:
License

This work is licensed under a Creative Commons Attribution-NonCommercial-NoDerivatives 4.0 International License.